Enhancing Overall Equipment Effectiveness (OEE) in Compressor Manufacturing Industries by Sripriyan K in Research & Development in Material Science_journal of materials processing technology
Abstract
This paper focuses on the methodology of improving the productivity through overall equipment effectiveness (OEE) with help of lean manufacturing technique in compressor manufacturing industries. For a good manufacturing plant, the most recommended things are quality and efficiency. These two parameters depend on the function of equipment used in the industry. In the current global competitive environment it is of immense importance for manufacturing companies to keep track of, and improve the production performance of their production systems. Production failure includes many reasons, among them improper maintenance and equipment performance are the eye catching reasons. Lean manufacturing techniques is to significantly identify the waste and eliminate it from the manufacturing processes. The OEE calculation is one of the ways to improve the performance. This work has been carried out in 2hp air compressor manufacturing unit for improving OEE with help of 5s techniques using a systematic approach The project has been addressed in three aspects; namely Availability, Performance and Quality which quantify OEE. The investigation result shows that the OEE has been improved from 45.9% to 55.8%.
Keywords: 5S; Overall equipment effectiveness (OEE); Standard operating procedure and Productivity.
Introduction
CThe manufacturing and process industry use Overall Equipment Effectiveness (OEE) as an important Key factor to monitor and control their performance effectiveness. At present the level of competition between firms is increasingly demanding, levels of demand by the customer are more stringent so that only the companies that have the ability to adapt easily to these needs are protruding. Maintenance plays a very important role in the industry, since to be able to produce goods of quality and quantity, and to deliver at the right time according to customer needs; machinery and equipment must operate efficient and accurate. Although it is not always recognized as an important area, maintenance has been widely regarded as a support function that is not productive, since it does not generate cash directly and sometimes relegated for that reason. OEE is a measure used in Total Productive Maintenance (TPM) to indicate how efficiently the machines are working. With the proper implementation of lean tools, the problems can be solved effectively and the productivity can be increased. The paper discusses about the analysis and implementation of lean tools for improving the overall equipment effectiveness and to meet the customer demand by using standard operating procedure and 5S techniques. 5S is a system which helps to organize a workplace for efficiency and optimizes quality and productivity via monitoring an organized environment.
Problem Definition
Data collection is done based on 2 hp air compressor manufacturing unit. The results show that while the setup time is more. Further observation revealed that they are not meeting the customer demand, because there is no proper assembly of workstations it will increases the manufacturing lead time. Another observation is the machine downtime is more because of improper maintenance. This will causes the less productivity. In machine shop there is no proper handling of 5S activity, this causes for more tool searching time for operators. It will also increase the non value added activity for operators in machine shop. Machine utilization also poor because of improper operating procedure. It will causes for less production.
Objectives
a. To reduce the non value added activity for operators in machine shop
b. To improve the overall equipment effectiveness
c. To meet the customer demand
To attain the above objective proper time study has been contacted and observations are noted down. Takt time is calculated and time study is done for each and every activity details are in Tables 1 & 2 [1,2]. The time study is done for each and every activity. Table 2 gives the details about the data collection. This data is tabulated based on average values noted.
Table 1: Takt time calculation.

Table 2: Time study observations.

Results and Discussion
After implementing lean tools OEE is improved 17.7% and productivity also increased from 35 products per shift to 40 products per shift details are in below.
Implementation Of Lean Tools
Different lean tools are identified to improve the OEE and productivity. After identification of lean tools, each tool is implemented as given below [3-6]:
Table 3: Implementation of lean tool.

Figure 1: Implementations of lean tool.
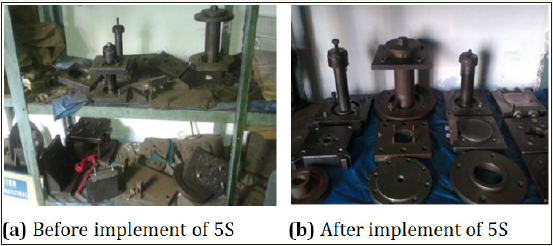
5S: 5S encourages workers to improve their working conditions and helps them to learn to reduce waste. In this paper 5S is one of the most important lean tools used. By using 5S as a tool lot of time is saved. The Table 3 and Figure 1 shows the details of before and after implement of lean tools.
Overall equipment effectiveness:
Overall equipment effectiveness for before implementation
An experimental result shows the compressor manufacturing unit having 45.9% of overall equipment effectiveness before implementation of lean tools details are in Table 4 & 5 and Figure 2. An experimental result shows the compressor manufacturing unit having 55.8% of overall equipment effectiveness before implementation of lean tools details are in Table 6-8 and Figure 3 & 4. After implementing each tool step by step the suitable results are found out and results are discussed as follows. Figure 4 shows the tool searching of operator after the implementation of 5S. By implementing lean tools suitable results are found out. There is reduction in setup time is found out. Table gives the clear picture of how much time is reduced (Table 9 & 10).
Table 4: Production data for before implementation

Table 5: Calculated data for before implementation.
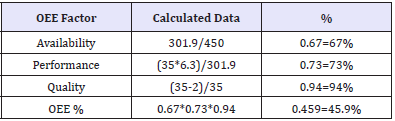
Figure 2: Overall equipment effectiveness for before implementation of lean tool.

Table 6: Downtime calculation for after implementation.

Table 7: Production data for after implementation.

Table 8: Calculated data for after implementation.

Figure 3: Tool searching time (Before).

Figure 4: Tool searching time (Before).
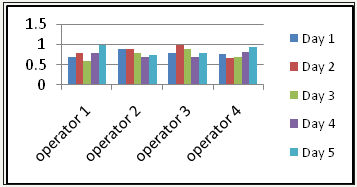
Table 9: Comparison OEE.

Table 10: Results comparison.

Conclusion
This paper was aimed to improvement of investigate the influences of the overall equipment effectiveness in compressor manufacturing unit. To this purpose, Tool Searching time, Downtime, Productivity and OEE are implemented and analyzed. Investigated results are compared before and after implementing the lean tools. The end results shows that 75% reduction of tool searching time, 23% down time reduction, productivity has increased 12.5% and 17.7% increasing the Overall Equipment Effectiveness.
References
- Bain N (2010) The consultants guide to successfully implementing 5S.
- Singh R, Gohil AM, Shah DB, Desai S (2013) Total productive maintenance (TPM) implementation in a machine shop: a case study. Procedia Engineering 51: 592-599.
- Sripriyan K, Janagiraman R (2001) Line balancing technique for labor optimization and productivity improvement in a compressor manufacturing industry. International Journal of Advanced and Innovative Research 4(4): 631.
- Matt DT, Rauch E (2009) Implementation of lean production in small sized enterprises. Procedia CIRP 12: 420-425.
- Escalante JE (1999) Quality and productivity improvement: a study of variation and defects in manufacturing. Quality Engineering 1(3): 427- 442.
- Sripriyan K, Janagiraman R (2018) Analysis and implementation of lean tools for lead time reduction in a compressor manufacturing industry. National Journal of Technology 11(3): 0973-1334.
No comments:
Post a Comment